We are in Marco’s workshop, who has lived surrounded by wood since he was born and continues running his father’s Francesco workshop. His story has its origins in 1968 when a group of siblings (amongst them Francesco) after finishing school at the cabinet-making school, following an internship in various companies of Verona,
This was a period in which everyone started to open their own shops and business, therefore they decided to open their own shop. Initially they worked by hand to make the 700’ trumeau style (a typical 700s Venetian dresser in Baroque style) Francesco and his brothers went to the pizzerias to take the olive trees to make the briar, it was an excellent material. He worked with only 3 machines: a cutter, a planer and a saw. There were 15 of them and they worked mainly by measure and by hand, then as the machines increased, the amount of workers decreased . Francesco tells us that on Saturday they loaded the furniture onto a cart tied to the bicycle and carried them around the nearby countryside to sell them.
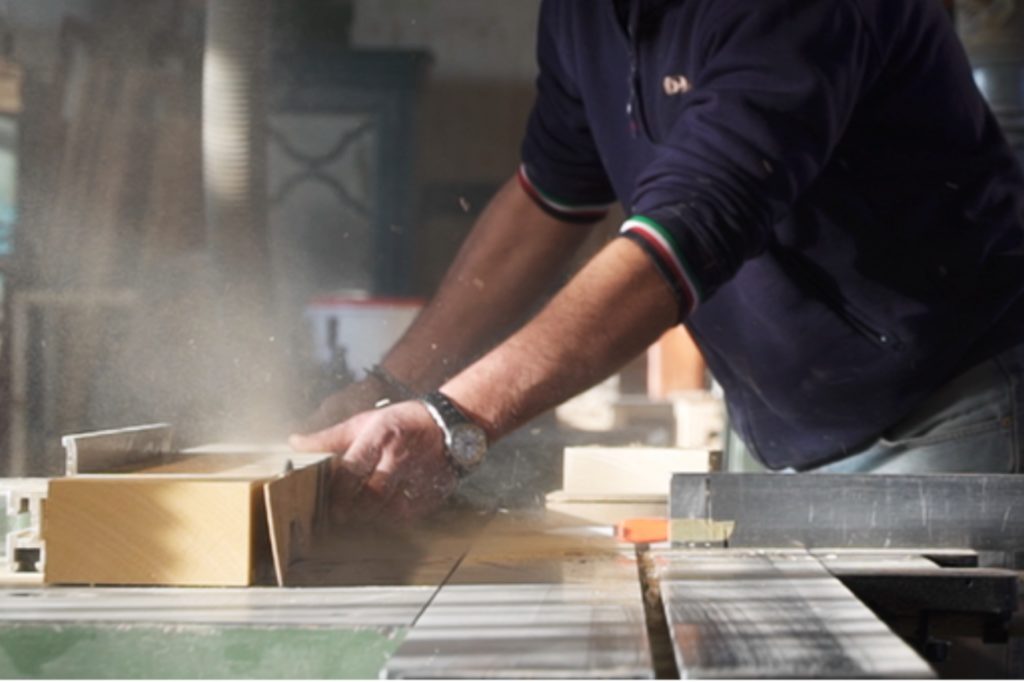
Tell us about yourself, about the places where you grew up, and how your workshop was born.
Until 1999 Marco was an accountant, but he took over his father’s company. Marco has always worked making customized furniture. His workshop has a strong artisanal connotation, but unlike the time when his father ran the workshop, currently, the design area is completely digital. During his first 10 years working at the workshop, he made kitchen designs and furniture completely by hand. “This was all happening in Verona, in the province area, 60 years ago. During this time, every door you’d see was a shop. The artisan in charge of the chair, someone else in charge of the carvings, whoever was in charge of polishes, people came from all over Italy to get their furniture made there”, says Marco’s father. Until the early 2000s, there were around 6000 furniture factories in the area, currently, there are around 1500 and they are the only ones that remain as a handmade building furniture shops, they are the last family. It all started with Maggiolini, the first cabinet maker in the area. Until the 1960s, this area was completely rural, filled with livestock and agriculture production, then there was the boom. I began working from home with a team of other men from the area, and from there the whole sector branched. Merlin’s M brand became a famous icon, and everyone copied it in the area since this symbol was equivalent to prestige and quality in furniture making.
There were about twenty companies in the town, but eventually, they were all closed: mostly the carver’s shops and workers of the briar, a style that went out of fashion during that time. From the end of the nineties until 2002 there was a collapse in the furniture-making world. From the trends that favored the “Furniture of Art” style to a more modern style. Furthermore, during the economic boom in Italy, everybody was building huge houses, so there was a need to have lots of furniture. Nowadays houses are small and there are other furniture needs. A good thing was that there was nothing in this area, therefore locals worked to find intelligent solutions. A common quality of Venetian culture.
Which tool do you use the most and what techniques do you use?
Here we still have a strong sense for artisan production, and I still work mainly by hand. I have strong skills as a carver. I use the techniques I learned from my father to create particularly special furniture legs. The saw the planner and the woodcutter are all instruments I learned to use from my father. Also freehand drawing. Afterwards, I began drawing my designs digitally.
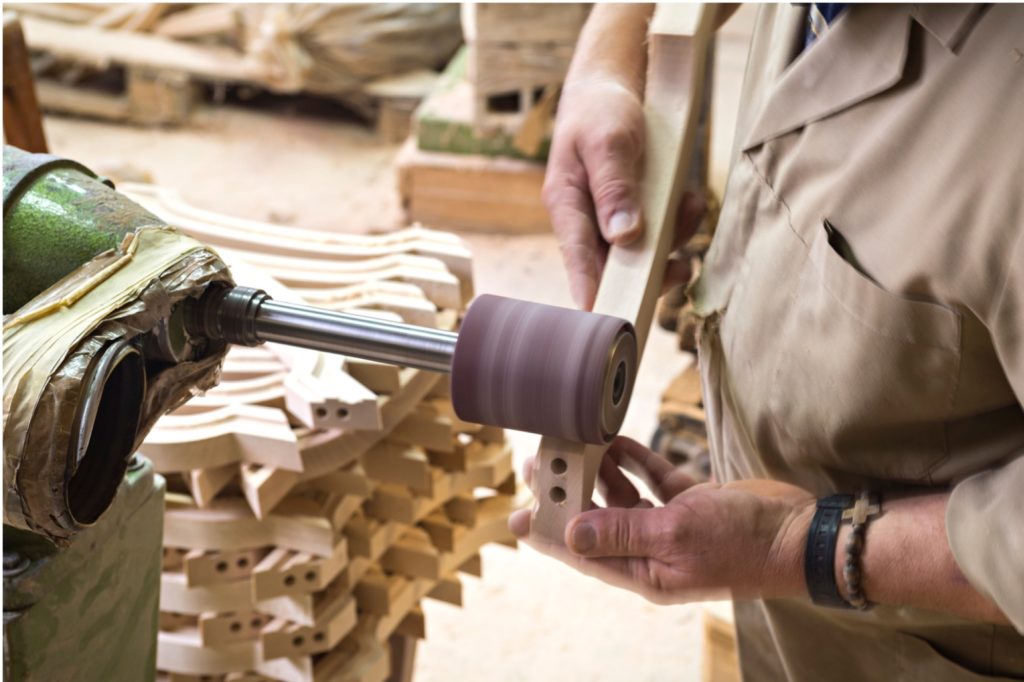
What do you enjoy doing the most in your craft? When is the best moment of your work?
Marco’s favorite thing about his craft is when he receives new designs, or when he creates them. Another moment he enjoys is when he finds different solutions to problems, the way a piece or a design might have. Free-hand design of a furniture piece, or a 3D furniture piece. Marco recently acquired a modern machine he learned to use even though it’s a technologically complex machine, a machine that is able to make vectorial designs of furniture and afterward built by the same machine.
How do your projects begin, you start with a design, and what happens afterward?
It starts with a hand-drawn design, you take the measurements, and afterward, everything is placed in the computer, afterwards, you design the furniture’s plans, then you create a 3D design with a vectorial program. A few years ago I had the courage to make a large investment, in an innovative machine that allows me to solve a series of errors and limits that previous machines would easily make. Without a technical background, I spent several nights (Christmas included) learning how to use it. It was thanks to this that I was able to update and revolutionize the way I created my pieces. Currently, I can place a technical design into the machine, and it can create pieces that I will be able to use to build the furniture by hand. Francesco created a tradition, Marco followed in his steps, and thanks to his foundations he continued with his work, currently with the help of innovations such as modern machinery he gets huge support when projecting and building furniture pieces.
What does “Made in Italy” represent to you?
Made in Italy means tradition, history, and the pursuit of taste and beauty, thanks to one’s own hands, taking into consideration the past, and tradition of the elder masters and integrating this with technology. Today this is what Made in Italy means. This is why we also love and enjoy restoring, and refreshing the beauty of antiquity by restoring it. Marco and Francesco are also the official restorers from a Veronese museum, from which they have restored furniture pieces, among them a table from Dante Alighieri’s last descendent.
What capacities have you acquired from your father?
“I learned to work by hand, the way my father (Francesco) did sixty years ago. Everything was hand made, and much of the machinery we have these days didn’t exist back then. We created the outlines for the wood frames from iron shapes. He also taught me many tricks to avoid getting hurt or cutting my hands.” The shop where Marco worked was much more advanced technologically than other furniture shops, many woodworkers were without fingers due to accidents on the job. Francesco was able to teach many things about the craft to his son, Marco: to work with the instrument in a hidden position to avoid placing them inside the machinery, mainly because hands are everything in this craft. In wood carving it’s still necessary to do many things by hand, for instance, if a piece needs to be sawn, it has to be accompanied by hand, therefore one must be extra careful.
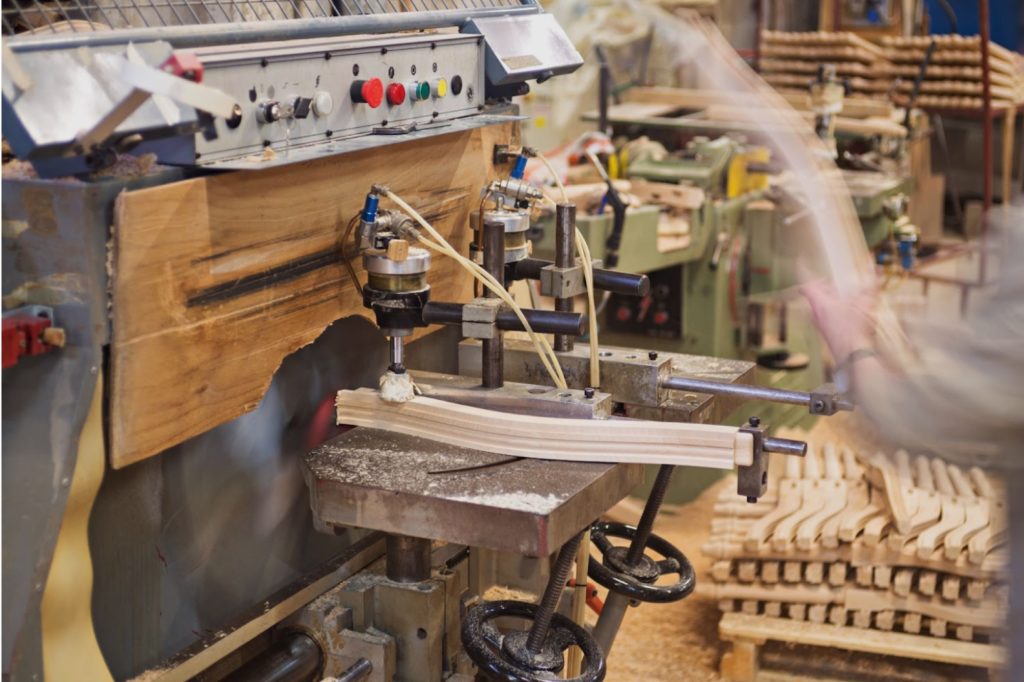